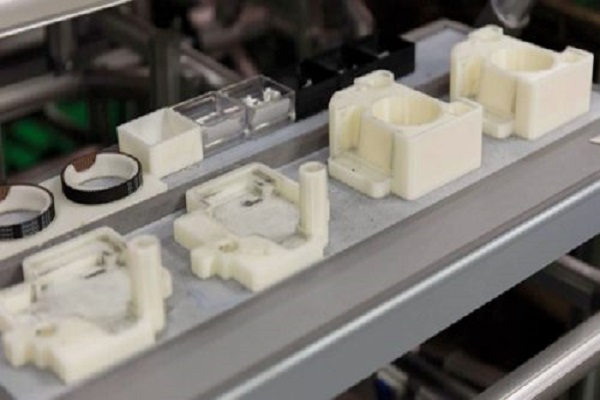
Ricoh Japón está sustituyendo las herramientas metálicas tradicionales de la línea de montaje de su Centro de Tecnología de Producción por guías y fijaciones personalizadas impresas en 3D con tecnología Stratasys. De esta forma, Ricoh mejorará su eficacia y reducirá al mínimo los problemas asociados a la fabricación manual de herramientas. En esta línea de montaje, situada en la delegación nordeste de Ricoh Industries, en la prefectura de Miyagi (Japón), se fabrican impresoras de gran formato.
Ricoh produce herramientas duraderas en termoplástico ABS en su impresora 3D Fortus 900mc de la serie Production de Stratasys, lo que le permite personalizarlas para que se adapten con precisión a la geometría de las piezas y reducir el peso. De esta manera, Ricoh ha agilizado el proceso de fabricación, en el que cada operario maneja normalmente más de 200 piezas al día.
La compañía desarrolla y fabrica equipos de oficina de alta calidad como, por ejemplo, copiadoras, máquinas de fax y proyectores. Dada la naturaleza competitiva del sector de componentes electrónicos, la empresa ha tenido que buscar nuevas formas de agilizar el lanzamiento de productos manteniendo los costos de producción o incluso reduciéndolos.
“Como producimos una gran cantidad de piezas, identificar las guías y fijaciones adecuadas para cada una de ellas requiere mucho tiempo y esfuerzo. Este proceso manual se prolonga aún más si aumenta el número de componentes, porque el operario tiene que examinar la forma, la orientación y el ángulo de cada pieza antes de sacar una herramienta y colocarla de nuevo en su fijación original. A veces, los operarios se mostraban descontentos debido al elevado número de herramientas diferentes, así que buscamos una forma de acelerar la fabricación de herramientas para adaptarla a nuestro programa de producción”, comenta Taizo Sakaki, director de Desarrollo de Negocio del Grupo Ricoh.
Antes de la llegada de la impresión 3D, Ricoh tenía que subcontratar la fabricación de herramientas de corte, un proceso que podía durar dos o más semanas. Actualmente, los operarios de Ricoh pueden determinar la forma y geometría de la fijación de la pieza asociada mediante software CAD 3D e imprimirla en 3D en un día.
En consecuencia, los trabajadores tienen más tiempo para ocuparse de otras tareas. Además, los nuevos empleados pueden adaptarse a las herramientas y estaciones de trabajo en dos días, mientras que antes necesitaban como mínimo una semana para familiarizarse con todas las herramientas. Las guías y fijaciones son también mucho más ligeras, por lo que los operarios pueden usarlas durante más tiempo sin cansarse.
“La solución de impresión 3D Stratasys Fortus 900mc nos permite realizar diseños difíciles de conseguir con los métodos de corte convencionales como, por ejemplo, interiores huecos, curvas o formas complejas. El material empleado para imprimir las herramientas en 3D es muy resistente y antiestático, algo muy importante dado el gran número de componentes electrónicos que montamos, y constituye una ventaja más de la impresión 3D de Stratasys”, explica Sakaki.
La planta de montaje de impresoras de gran formato de Ricoh ha sido pionera en la adopción de la fabricación digital. La empresa sigue explorando campos de aplicación de la impresión 3D, como el moldeo y la producción de bajo volumen, para agilizar los flujos de trabajo y de esa forma poder liberar más recursos y ampliar la cartera de productos que ofrece a su variada base de clientes.
“Ricoh está encantada de liderar la adopción de esta tecnología en nuestro sector. Nuestro espacio de trabajo es ahora más flexible y está mejor organizado, y los operarios de la línea de montaje están encantados”, comenta Masami Hirama, director del Centro de Innovación de Producción de Ricoh.
[wp_ad_camp_1]